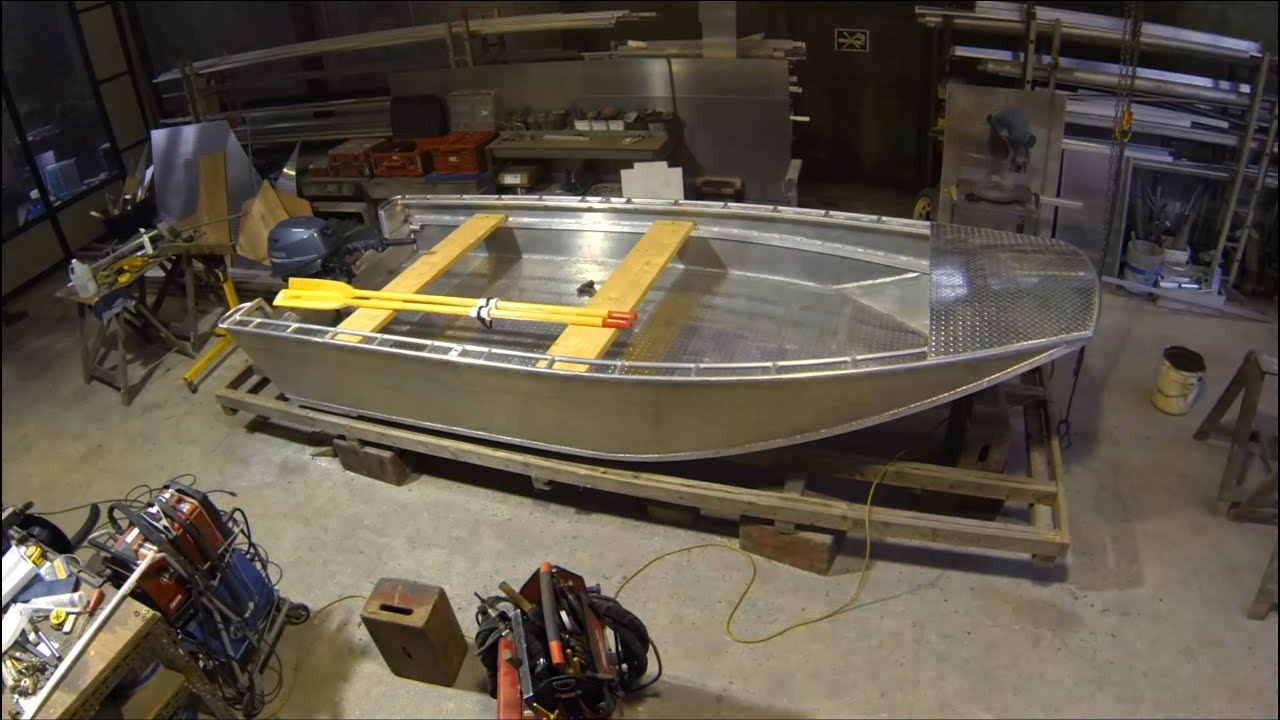
Building a Watertight Aluminum Boat: A Comprehensive Guide
Constructing an aluminum boat requires meticulous attention to detail, particularly regarding watertight integrity. A leak, however small, can compromise the vessel's safety and functionality. This comprehensive guide outlines the essential steps and considerations for ensuring your aluminum boat remains watertight throughout its lifespan. From initial design to final sealing, each stage demands precision and adherence to best practices.
I. Design and Material Selection: Laying the Foundation for Watertightness
The foundation of a watertight aluminum boat lies in its design and the selection of appropriate materials. Careful planning minimizes potential leak points and maximizes structural rigidity, thereby enhancing watertightness.
A. Optimal Design Considerations
Minimizing Joints and Welds: The more welds and joints in the boat's structure, the greater the potential for leaks. A well-designed boat should incorporate large, continuous sheets of aluminum wherever feasible, reducing the number of seams and enhancing structural integrity. Consider using computer-aided design (CAD) software to optimize the design for minimal joints.
Reinforced Seams and Joints: Where joints are unavoidable, they must be meticulously reinforced. This can be achieved through the use of backing plates, gussets, and strategically placed rivets or welds. The type of reinforcement should be determined based on stress analysis specific to the design.
Proper Drainage Design: Incorporating effective drainage systems is crucial for managing water ingress. This includes self-bailing cockpits, scupper holes, and bilge pumps. The placement and size of these features should be carefully considered to ensure efficient water removal.
Hull Shape and Stability: The hull design plays a vital role in watertightness. A robust, well-designed hull can better withstand impacts and stresses that could cause leaks. Consider the use of a multi-chine hull for greater strength and stability. Hydrostatic pressure calculations should be performed to ensure the hull can withstand the forces imposed by water.
B. Selecting Appropriate Aluminum Alloys
The choice of aluminum alloy significantly impacts the boat's durability and resistance to corrosion, both of which are crucial for long-term watertightness. Marine-grade aluminum alloys, such as 5052 or 5086, are recommended due to their superior corrosion resistance in saltwater environments. These alloys offer a balance of strength and weldability, essential for constructing a robust and leak-free structure.
Thickness Considerations: The thickness of the aluminum sheets should be carefully determined based on the boat's size, intended use, and anticipated stress levels. Thicker aluminum provides greater strength and stiffness, reducing the likelihood of damage and subsequent leaks. This requires careful consideration of weight as thicker aluminum increases the overall weight of the boat.
II. Construction Techniques: Precision and Meticulous Execution
The construction phase requires rigorous adherence to proper techniques to ensure watertight seams and joints. Improper welding or riveting can compromise the boat's integrity, leading to leaks.
A. Welding Techniques
Qualified Welders: Aluminum welding requires specialized skills and expertise. It's crucial to employ certified welders proficient in Gas Tungsten Arc Welding (GTAW), also known as TIG welding, which is preferred for its superior weld quality and aesthetics. MIG welding is an alternative but may require post-weld grinding and finishing for improved leak prevention.
Weld Penetration and Bead Appearance: The welder must ensure complete penetration of the weld, creating a strong, continuous joint. The bead should be smooth, consistent, and free from porosity or cracks. Any imperfections should be addressed immediately through grinding and re-welding.
Pre- and Post-Weld Cleaning: Thorough cleaning of the aluminum surfaces before welding is essential to remove contaminants that can affect weld quality. Post-weld cleaning involves removing any spatter or slag to ensure a smooth, watertight surface.
B. Riveting Techniques
Proper Rivet Selection: Selecting the correct size and type of rivet is critical. Aluminum rivets are typically used and should be appropriately sized for the thickness of the aluminum sheets being joined. Solid rivets generally provide superior strength and watertightness compared to blind rivets.
Even Rivet Spacing: Maintaining consistent rivet spacing along seams and joints is essential for distributing stress evenly. Uneven spacing can create stress concentrations, leading to potential leaks.
Rivet Setting and Sealant: Rivets should be set firmly and evenly to ensure a tight, watertight joint. A sealant, such as a high-quality marine-grade sealant, should be applied around the rivets to further enhance watertightness.
III. Sealing and Finishing: Ensuring Lasting Watertightness
Even with perfect welds and rivets, a final sealing process is crucial to prevent water ingress through microscopic gaps or imperfections.
A. Sealant Application
Marine-Grade Sealants: Use only high-quality, marine-grade sealants specifically designed for aluminum and underwater applications. These sealants are formulated to resist corrosion, UV degradation, and the harsh marine environment.
Proper Sealant Application: Apply the sealant evenly and generously along all seams, joints, and around rivets. Ensure the sealant completely fills any gaps or imperfections. Follow the manufacturer's instructions for cure time.
B. Surface Preparation and Finishing
Surface Cleaning: Before applying any sealant or paint, thoroughly clean the aluminum surfaces to remove any dirt, grease, or contaminants. This is critical for proper sealant adhesion.
Primer and Paint: Applying a suitable primer and marine-grade paint provides additional protection against corrosion and enhances the boat's longevity. Multiple coats are generally recommended.
IV. Testing and Inspection: Verifying Watertight Integrity
Thorough testing and inspection are crucial to ensure the boat is fully watertight before launching. This involves various methods to detect and address even minor leaks.
A. Pressure Testing
Pressure testing involves filling the boat with water and carefully inspecting for any leaks. This can be done by inflating the hull to a predetermined pressure. Any water escaping from seams or joints will indicate the need for repair.
B. Leak Detection Techniques
Employ leak detection techniques such as using a dye penetrant to reveal any hairline cracks or leaks in the welds or seams. Following this, a pressure test can be performed to fully confirm the location and severity of any potential leak.
C. Visual Inspection
A thorough visual inspection is crucial after welding, riveting, and sealing. Examine all joints and seams for any visible cracks, gaps, or imperfections. Address any imperfections promptly.
Building a watertight aluminum boat demands a combination of meticulous design, precise construction techniques, and thorough testing. By adhering to the principles outlined in this guide, you can significantly enhance the chances of creating a safe, durable, and leak-free vessel capable of withstanding the rigors of the marine environment. Remember to always consult with experienced professionals and adhere to all relevant safety regulations throughout the construction process.
0 comments:
Post a Comment
Note: Only a member of this blog may post a comment.